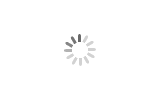
GM-Ⅰ-Ⅱ-Ⅲ Spezielle Korrosionsschutzserie
Die GM-Serie bietet außergewöhnliche Korrosionsbeständigkeit: GM-Ⅰ widersteht aggressiven Chemikalien (6+ Jahre), Stößen/Biegen und extremen Temperaturen (-40 °C bis 150 °C) und verfügt über eine 100 % geschlossenzellige, umweltfreundliche Formel. GM-Ⅱ wurde für farbige Stahlfliesen entwickelt und zeichnet sich durch UV-Beständigkeit, Vergilbungsbeständigkeit und einfache Anwendung aus. GM-Ⅲ nutzt fortschrittliche Technologie zur Verhinderung von Vergilbung (500 Stunden lichtecht) und verbindet Ästhetik mit Langlebigkeit. Alle Varianten sind lösungsmittelfrei, trinkwasserzertifiziert und ideal für chemische, maritime und kommunale Anwendungen.
Merkmale der Produktreihe
1. GM-Typ I-001 Spezielle Korrosionsschutzbeschichtung
Hauptmerkmale:Außergewöhnliche Korrosionsbeständigkeit, hervorragende physikalische Eigenschaften, umweltfreundlich.Langfristige r
Beständigkeit gegenüber starken Säuren (5–50 % Schwefelsäure), starken Basen (gesättigtes Ca(OH)₂), Salzen und Lösungsmitteln, mit einer Korrosionsschutzwirkung von über 6 Jahren. Hohe Schlagfestigkeit (50 kg/cm²), ausgezeichnete Flexibilität (keine Risse auf einem Dorn mit ∅10 mm) und breite Temperaturtoleranz (-40 °C bis 150 °C). Lösungsmittelfrei, besteht Trinkwassersicherheitstests, 100 % geschlossenzellige Struktur.
Anwendungen:Lagertanks, Pipelines, Brücken, Offshore-Plattformen, Abwassertanks und andere stark korrosive Umgebungen.
2.GM-Typ II-002 Farbige Korrosionsschutzbeschichtung für Stahlfliesen
Hauptmerkmale:Vergilbungsfreies Design, einfache Anwendung, starke Witterungsbeständigkeit. Hohe Temperaturbeständigkeit (120 °C), niedrige Temperaturbeständigkeit (-30 °C), 100 % geschlossenzellige Struktur. Überlegene UV-Alterungsbeständigkeit, deutlich verbesserte Farbstabilität. Geeignet für große flache Untergründe (z. B. farbige Stahlfliesen), kann direkt aufgetragen oder in Kombination mit Typ I verwendet werden.
Anwendungen:Erneuerung farbiger Stahlfliesen, Stahlkonstruktionsfabriken, Lagertanks, chemische Geräte usw.
3. GM-Typ III-003 Spezielle Anti-Vergilbungs- und Anti-Korrosionsbeschichtung
Hauptmerkmale:Verbesserte Vergilbungsbeständigkeit durch den Einsatz internationaler Technologie zur Vermeidung von Verfärbungen der Beschichtung (0-Grad-Kreidebildung nach 500-stündigem künstlichen Alterungstest). Verbund-Korrosionsschutzsystem, erfordert Typ I als Grundierung, schafft ein Gleichgewicht zwischen Korrosionsbeständigkeit und Ästhetik. Chemische Beständigkeit: widersteht 50 % Schwefelsäure, 10 % Salzsäure, 10 % NaOH usw.; besteht 500-stündigen neutralen Salzsprühtest ohne Rost.
Anwendungen:Schiffstechnik, kommunale Einrichtungen, Lebensmittel- und Pharmaausrüstung und andere Szenarien, die eine hohe Farbstabilität erfordern.
Vergleich der Leistungsparameter
Testgegenstand | GM-Typ I-001 | GM-Typ II-002 | GM-Typ III-003 |
Säure-/Basenbeständigkeit | Keine Veränderung nach 30-tägigem Eintauchen | Keine Veränderung nach 30-tägigem Eintauchen | Keine Veränderung nach 7-tägiger Immersion |
Temperaturbereich | -40 °C ~ 150 °C | -30 °C bis 120 °C | -30 °C bis 120 °C |
Haftung | 12 MPa (Abreißfestigkeit) | Klasse 1 (Kreisschnitt) | 10 MPa (Abreißfestigkeit) |
Schlagfestigkeit | Keine Risse bei 50 kg/cm² | Keine Risse bei 50 kg/cm² | Keine Rissbildung bei 50 cm |
Vergilbungs-/Alterungsbeständigkeit | Verfärbung Grad 2 nach 168 Stunden UV | Kreidungsgrad 0 nach 160h UV | Verfärbungsgrad 0 nach 500 Stunden UV |
Geschlossene Zellrate | 100 % | 100 % | 100 % |
*Die oben genannten Daten basieren auf tatsächlichen Formulierungen und Produkten.
Konstruktionsrichtlinien
▊ Oberflächenvorbereitung
Reinigen Sie den Untergrund gründlich von Öl, Fett und Rost und stellen Sie sicher, dass er trocken ist (Feuchtigkeitsgehalt ≤ 8 %). Reparieren Sie bei Zementuntergründen alle Risse. Bei Metalluntergründen empfiehlt sich Sandstrahlen oder Schleifen.
▊ Beschichtungsvorbereitung
Mit einem elektrischen Rührgerät gleichmäßig vermischen und 10–15 Minuten stehen lassen. Bei Typ III zuerst Grundierung Typ I auftragen (24 Stunden Trocknungszeit einplanen).
▊ Anwendungsmethoden
Mit Pinsel, Rolle oder Spritzgerät auftragen, mit einer Einzelschichtdicke von 0,1–0,2 mm und einer Gesamtdicke von 0,3–0,5 mm. Zwischen den Schichten 24 Stunden warten (bei Raumtemperatur, 25 °C).
▊ Umweltanforderungen
Temperatur: 5 °C–35 °C, Luftfeuchtigkeit ≤ 85 %. Anwendung bei Regen oder Schnee vermeiden.
Vorsichtsmaßnahmen
(1) Tragen Sie während der Anwendung Schutzhandschuhe, Masken und Schutzbrillen und sorgen Sie für ausreichende Belüftung.
(2) Reinigen Sie die Werkzeuge nach der Konstruktion umgehend mit einem speziellen Verdünner, um eine Verfestigung der Beschichtung zu verhindern.
(3) Verwenden Sie während der Anwendung Schutzausrüstung wie Handschuhe, Masken und Schutzbrillen.
(4) Sorgen Sie für ausreichende Belüftung am Arbeitsplatz, um das Einatmen schädlicher Dämpfe zu vermeiden.
Lagerung und Transport
Artikel | Erfordernis |
Lagerbedingungen | An einem kühlen, trockenen und gut belüfteten Ort aufbewahren, fern von direkter Sonneneinstrahlung und hohen Temperaturen |
Lagertemperatur | Zwischen 5 °C und 35 °C halten; Einfrieren vermeiden |
Haltbarkeit | 12 Monate (ungeöffnet) |
Transportzustand | Vermeiden Sie starke Vibrationen und Stöße, um eine Beschädigung der Verpackung zu verhindern |